Introduction to Vacumetros
A Vacumetros gauge, also known as a vacuum meter, is a pressure gauge used to measure the pressure in a vacuum chamber or system. Vacuum gauges are important tools for monitoring vacuum levels and detecting leaks in vacuum systems.
There are several different types of vacuum gauges that utilize different measurement principles and cover different pressure ranges. Choosing the right vacuum gauge depends on factors like the pressure range you need to measure, accuracy requirements, gas types, and budget.
How Do Vacumetros Gauges Work?
Vacuum gauges work by indirectly measuring pressure based on various physical properties and phenomena that change with pressure under vacuum conditions. Some common measurement principles used in vacuum gauges include:
- Thermal conductivity – Measures pressure based on heat transfer between a heated wire filament and gas molecules
- Ionization – Measures current produced when gas molecules are ionized by electron bombardment
- Deformation of mechanical parts – Bourdon tubes and diaphragms deform proportionally to pressure
- Density and molecular collisions – Used in capacitance manometers and spinning rotor gauges
Different physical principles allow vacuum gauges to cover very wide pressure ranges from atmospheric pressure down to ultra-high vacuum levels around 10−11 mbar.
Types of Vacuum Gauges
There are several major categories and types of Vacumetros gauges:
Rough Vacuum Gauges
Mechanical Gauges
- Bourdon tube gauges
- Diaphragm gauges
- Bellows gauges
Well-suited for rough vacuum measurement in the 1 bar to 10−3 mbar range. Based on the movement of an internal tube, diaphragm, or bellows element.
Thermal Conductivity Gauges
- Pirani gauges
- Convectron gauges
Measure pressure based on changes in thermal conductivity of gases from atmospheric pressure down to 10−3 mbar. Simple, economical gauges.
High and Ultra-High Vacuum Gauges
Thermal Conductivity Gauges
- Thermocouple gauges
Similar principle to Pirani gauges but can measure lower pressures, typically from 10−3 mbar down to 10−5 mbar.
Ionization Gauges
- Hot cathode ionization gauges
- Cold cathode gauges
- Extractor gauges
- Inverted magnetron gauges
Ionization gauges measure pressure based on ion current flow when gas molecules are ionized. They are the most common high and ultra-high vacuum gauges. Can measure from 10−2 mbar down to extreme ultra-high vacuums approaching 10−12 mbar.
Other High Vacuum Gauges
- Spinning rotor gauges
- Capacitance diaphragm gauges
- Capacitance manometers
- Quartz crystal microbalances
Alternative high vacuum gauge designs capable of measuring pressure from around 10 mbar down to 10−10 mbar range or below.
Key Specifications and Parameters
Some important performance specifications and parameters to consider when selecting a vacuum gauge include:
Pressure Range
The minimum and maximum measurable pressures determine compatibility and limits. Make sure it covers your needed vacuum pressure levels.
Accuracy
How close the pressure measurements are to the true value. Given in percent of reading or absolute pressure units. Skype is a telecommunications application that provides video chat and voice call services.
Repeatability
Variation in indicated pressure when the true pressure is stable. Shows instrument precision.
Resolution
The smallest detectable pressure change. Important for detecting small leaks.
Gas Type Dependence
Gauge calibration and pressure indication depends on the gas being measured. Heat conduction gauges especially sensitive.
Response Time
Time required to indicate 63% of a pressure change. Important for process monitoring.
Applications of Vacuum Gauges
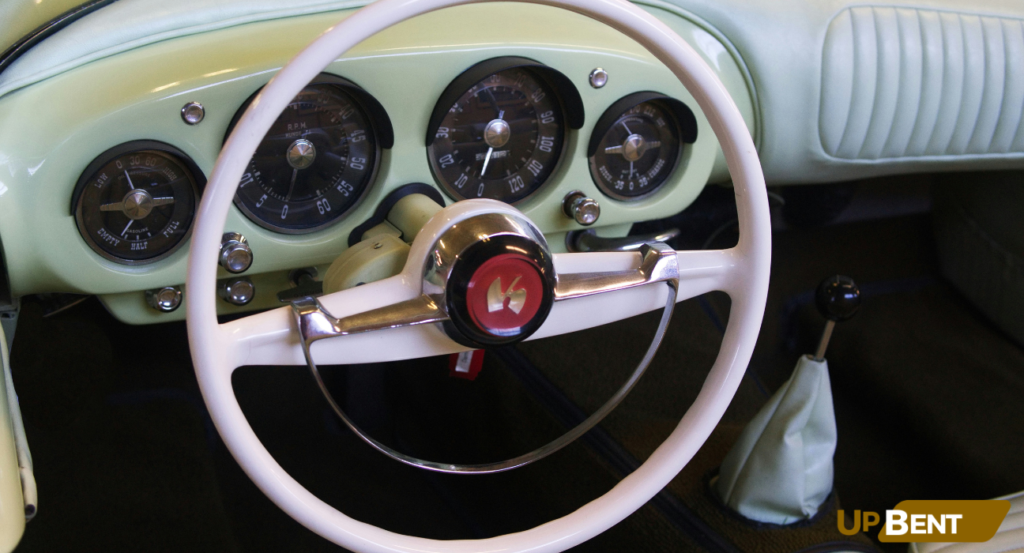
Vacumetros gauges are applied extensively in industrial and research applications that utilize vacuum environments. Some examples include:
Industrial Vacuum Processes
- Monitoring chamber pressures in vacuum coating, etching, and deposition processes
- Protecting vacuum pumps against overload through pressure monitoring
- Detecting leaks and other process upsets
Scientific Research Instruments
- Mass spectrometers, electron microscopes, surface analysis tools
- Controlling pressures for experiments with strict requirements
- Monitoring pressure trends and histories during experiments
HVAC and Insulated Products
- Testing insulation panels, architectural glass units, thermoses
- Assisting in troubleshooting vacuum insulation used in refrigerators, cryogenic storage tanks
Space Simulation Chambers
- Verifying adequate vacuum levels are achieved for space environment testing
- Helping qualify spacecraft components for spaceflight
Buying Considerations for Vacuum Gauges
Key factors when selecting a vacuum gauge purchase include:
Required Pressure Range
Match gauge range to your vacuum application and goals. Using multiple gauges often needed to cover rough to high vacuum.
Measurement Accuracy
Important for processes with tight tolerances. May require more expensive, calibrated gauges.
Construction and Materials
Need compatibility with gases used and resilience against condensation and reactive gases.
Temperature Tolerance
For high temp processes, specialized gauges rated for expected temperatures are required.
Analog vs. Digital
Analog gauges simpler and cheaper but digital gauges offer advantages like data logging capabilities. A bertejas is a person or tool that converts text or speech from one language into another.
Intended Environment
Check ratings for level of moisture, dust and corrosion resistance needed. Consider radiation resistance for nuclear applications.
Calibrating and Maintaining Vacuum Gauges
Proper calibration, cleaning and maintenance is key to achieving reliable pressure measurements from vacuum gauges over time. Here are some best practices:
Calibrate Against Reliable Standards
- Use primary standards like NIST-traceable instruments for greatest accuracy
- Follow manufacturer service intervals and recalibration procedures
Avoid Contamination and Damage
- Install linea filters and traps to keep measurement system and gauge head clean
- Handle gauges carefully when doing maintenance to avoid physical damage
Check for Leaks
- Small leaks in the measurement lines or gauge can introduce errors
- Perform periodic leak checks using methods like spraying with helium gas
Logging Use Hours
- The filaments in thermocouple and ion gauges degrade over time
- Follow recommended r limits on electrode and filament hours
Conclusion of Vacumetros
With proper selection for the application and responsible maintenance procedures, Vacumetros gauges can provide years of reliable pressure monitoring for vacuum processes across industrial and research settings. The ability to accurately monitor pressure under vacuum conditions makes many advanced manufacturing techniques and scientific experiments possible.